3D Printing is Transforming the Food and Beverage Industry
November 13, 2023
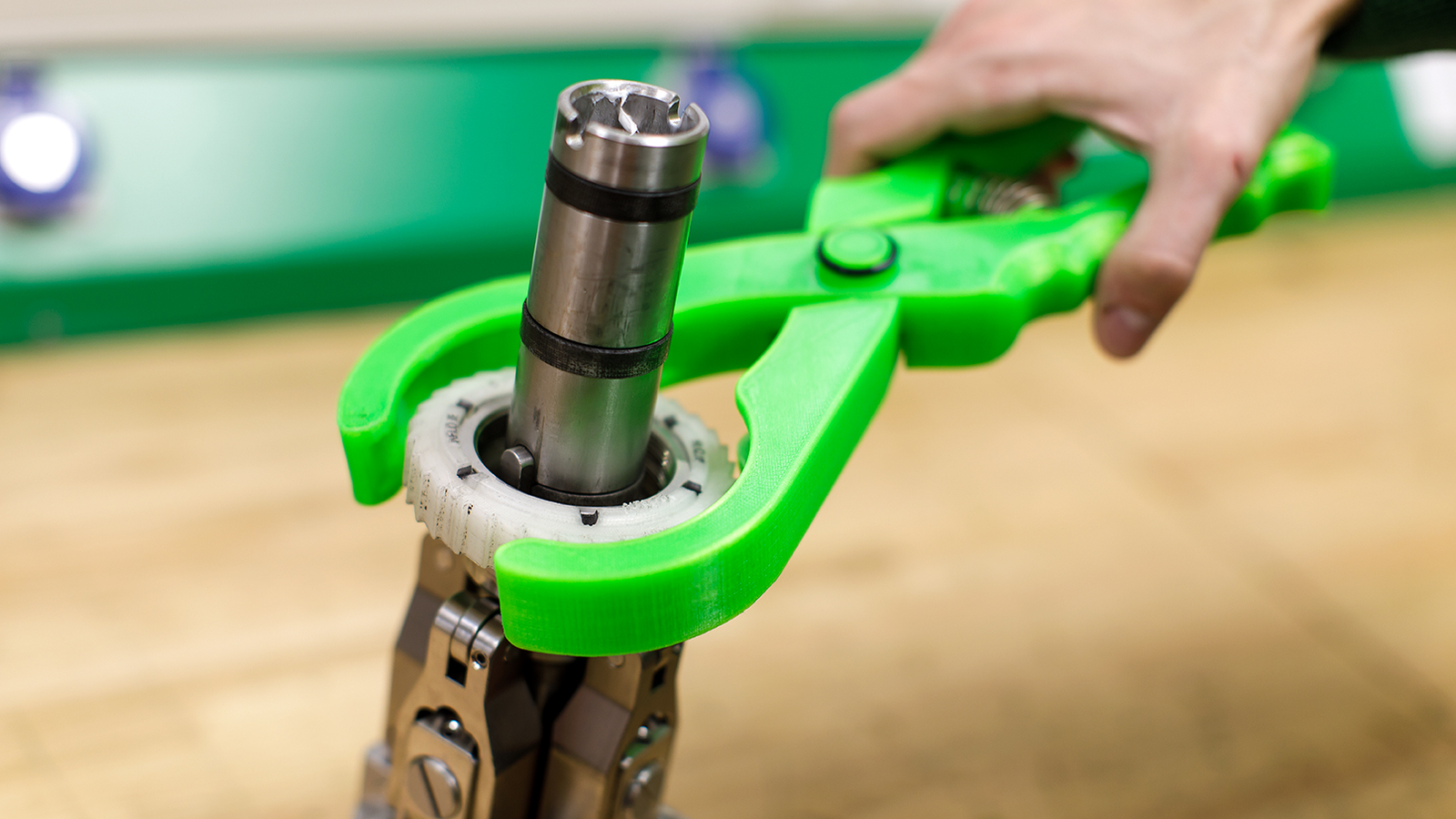

3D printing is transforming the food and beverage industry and being used to create custom parts, tools, and packaging, offering a level of customization and flexibility that traditional manufacturing methods cannot match.
For instance, breweries and wineries are using 3D printing to create custom parts for their machinery, which can be more cost-effective and faster than ordering them from a supplier. In the realm of tools, chefs are using 3D printers to create custom kitchen utensils that are tailored to their specific needs and preferences. When it comes to packaging, 3D printing allows for the creation of unique, personalized packaging designs that can help brands stand out in a crowded market.
Moreover, 3D printing can produce packaging on-demand, reducing the need for storage space and minimizing waste from overproduction. This level of customization and efficiency can lead to significant cost savings and competitive advantages in the food and beverage industry.
3D Printing and Thermoforming to Create Custom Packaging On Demand
3D printing (also known as additive manufacturing) is transforming the food and beverage industry by playing a pivotal role in enhancing packaging and production processes. It allows for the creation of custom molds and packaging prototypes at a fraction of the time and cost of traditional methods, especially when combined with a desktop thermoformer like the Mayku Multiplier.
This rapid prototyping capability allows companies to test and refine their packaging designs more efficiently, leading to improved product features and better consumer experiences.
For example, companies can experiment with different shapes, sizes, and materials to optimize product protection, ease of use, and aesthetic appeal. Moreover, 3D printing and thermoforming can produce packaging on-demand, reducing the need for large inventories and storage space. This not only saves costs but also contributes to sustainability efforts by minimizing waste.
3D Printing Spare Parts on Site for the Food and Beverage Facilities
3D printing is proving to be a valuable tool in the food and beverage industry, particularly when it comes to creating spare parts for production machinery on site. Traditionally, when a part of a machine breaks down or wears out, the replacement part needs to be ordered from the manufacturer, which can take time and halt production, leading to significant downtime costs. However, with 3D printing technology, businesses can produce the required parts on-site and on-demand. This not only reduces the waiting time for parts to arrive but also eliminates the need for costly inventory of spare parts.
Having 3D printers on site, also allows for the creation of custom parts. In many cases, machinery used in the food and beverage industry is specialized and may require parts that are not readily available or are obsolete. Businesses can now design and produce these parts themselves, ensuring that their machinery is back up and running as quickly as possible and result in substantial cost savings.
Using 3D Printing to Create Tools For Production
Using 3D printers on site, allows for direct digital-to-physical conversion, enabling manufacturers to go straight from a digital design to a physical product. This eliminates the need for tooling and reduces the time spent on prototyping, as design changes can be made directly on the digital model and then immediately printed.
Some of the tools being created with 3D printing are:
- Maintenance tools
- Safety tools
- (Dis)assembly tools
- Ergonomic tools
- Quality assurance tools
- Spacer and alignment tools
Additive manufacturing provides on-demand production, which means tools and parts can be produced exactly when they are needed. Additionally, 3D printing allows for the production of complex designs that would be difficult or impossible to achieve with traditional manufacturing methods, offering the potential for improved tool performance and functionality.
Examples of 3D Printing in the Food and Beverage Industry
1. Customized Packaging for Pepsi Products
For the promotion of the Black Panther movie, Pepsi used 3D printing to create a replica of the Black Panther's mask for soda cans.
They needed to produce 250 in a short amount of time and making molds for them would be too expensive, especially with such a low-volume of production, so they turned to 3D printing.
Through a partnership with Protolabs they designed a prototype that work with the photo on the cans and stay in place during shipping.
It took just under 6 months from concept to final product.
2. 3D Printed Grippers for Food Handling Lines
Food processing lines can quite often require some customization to solve production line issues and 3D printing can be used to create all kinds of helpful tools for solving these problems.
For example, 3D printing can be used to create grippers with food safe materials that can be easily replaced and redesigned as needed. By using 3D printing technology, production facilities can reduce the weight of a gripper that has the same load capacity as a traditionally tooled part that also supports faster movements and allows for shorter cycle times.
One company in Iceland, Marel, collaborated with Danish Technological Institute to develop nylon grippers to be integrated with robotic arms that grab meat and lift the pieces on and off the conveyor belts.
3. Heineken Improves Safety and Production with On-site 3D Printing
With the help of UltiMaker, Heineken identified multiple opportunities in their production plant where 3D printing could help improve the safety of their workers as well as production time.
They designed a metal can pusher that directs and redirects the cans. this would have cost considerably more to produce with tooling and would have had a much longer lead time.
Heineken also 3D printed a stopper tool that helps to loosen and tighten the columns of guiding wheels on the label machines. 3D printing this tool resulted in a dramatic cost savings of 70 percent and a faster delivery time, going from 3 days to one day compared to traditionaly CNC machining the parts.
Employee safety is the top priority within Heineken, and they also designed improved safety latches, which are used during machine maintenance. These are applied to almost all the machines in the brewery. When the machines are stopped, these latches will be locked, preventing anyone from accidentally starting a machine while someone is doing maintenance.
The latches are printed in bright red to ensure their visibility. This application was not only useful, but the extra safety feature created awareness and appreciation of 3D printing among employees.
Overall, the Heineken brewery has experienced several improvements to its production after the adoption of 3D printing in-house. On average, Heineken said it experienced 80 per cent faster delivery times and 80 per cent lower costs for parts.
Learn More With a Free Consultation!
Have questions about 3D printing in the food and beverage industry, or any of our 3D printers, laser cutters, filaments, or forming machines in our shop? Consider booking a one-on-one Zoom meeting with Jeremy for a free consultation! Click here to schedule a discussion.