3D Printing Metal Parts
May 08, 2024
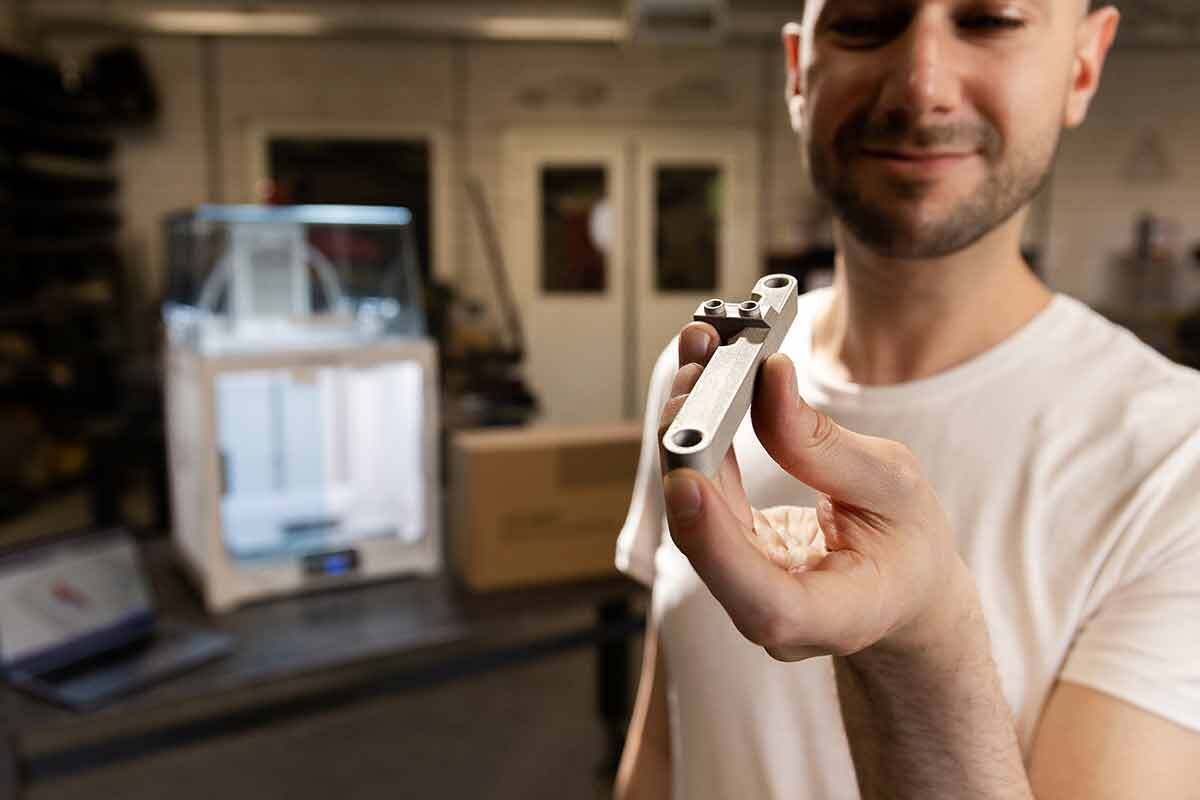
You're probably already aware that it's possible to 3D print real metal parts. But did you know this can now be done very affordably even with ordinary desktop 3D printers?
In this article, we'll explore several ways of 3D printing metal parts, including some options that you might not have realized were so affordable and accessible.
Direct Metal Printing (DMP/DMLS)
Direct Metal Laser Sintering (DMLS), also sometimes referred to as Direct Metal Printing (DMP), is a type of additive manufacturing technology that uses a laser to fuse together different layers of metal powder to form a solid, three-dimensional object.
Organizations that require the best-possible quality metal parts, such as those in the aerospace industry will want to explore Direct Metal Printing.
This kind of metal 3D printing offers many advantages:
- Fabrication of intricate parts unachievable with conventional manufacturing techniques
- Creation of conformal cooling channels and lattice structures
- Improvement of fluid dynamics
- Direct, tool-free fabrication of injection molding components such as inserts and cores
- Customized production of items like orthopedic and dental parts tailored to individual specifications
- Manufacturing of parts featuring cavities, undercuts, and draft angles
- Designing lighter components to reduce overall weight.
- Application in research and development projects
- Streamlining assemblies through the consolidation of multiple parts into fewer components
- Production of small, highly precise components
- Conducting topology optimization to ensure structural integrity while optimizing material distribution
Why is Direct Metal 3D Printing So Expensive?
Traditional Metal 3D printing, or Direct Metal Laser Sintering (DMLS), can be expensive for a wide variety of reasons:
Material Costs: The metal powders that are used in DMLS are very fine and pure, which makes them more expensive than the raw materials used in traditional manufacturing processes.
Machine Cost: The machines used for metal 3D printing are complex and high-tech, leading to high initial investment costs. They also require regular maintenance and calibration to ensure precision and reliability.
Post-Processing: Metal 3D printed parts often require additional post-processing steps such as support removal, heat treatment, and surface finishing. These steps add to the overall cost.
Energy Consumption: The process of sintering metal powder layer by layer is energy-intensive, which can contribute to higher operational costs.
Expertise: Operating a metal 3D printer and preparing designs for printing requires specialized knowledge and skills, which can add to labor costs.
Cutting Costs by Printing Metal Using Standard FDM printers
This method of producing metal parts starts with metal-infused filament that has a high percentage of metal powder mixed into a plastic base so it can be extruded using normal desktop 3D printers. The printed parts then go through a debinding process (to remove the plastic filler material) and then a sintering process (to fuse the metal particles together). The result is a solid metal part at a fraction of the cost of other manufacturing methods!
Some shrinkage does occur during the debinding and sintering process, but this is compensated for by applying some pre-defined scaling parameters to your object during the slicing process, resulting in a finished part that closely meets your design specifications.
Here at 3D Universe, we have two great solutions available for printing metal parts using common desktop 3D printers. As long as your printer has a heated bed and a hardened nozzle, chances are good that these methods will work for you!
One solution is to use BASF UltraFuse metal filaments. These materials require a specialized debinding process, so the printed parts need to be shipped to a 3rd party for debinding and sintering. Then they send the final metal parts back to you.
The other solution is to use The Virtual Foundry materials, available in a range of different metal types. These materials can be processed entirely in-house using a standard programmable kiln.
Let's explore each of these solutions in more detail...
BASF UltraFuse Metal Filaments for FDM 3D Printing
BASF Ultrafuse® 316L is an innovative filament to produce 316L grade stainless steel parts from existing FDM desktop 3D printers.
It is designed for ultimate ease of handling on conventional Fused Filament Fabrication (FFF) 3D printers. BASF Ultrafuse® 316L combines greater freedom of design with a lower total cost of ownership – printing metal parts easier, faster, and affordable. Parts printed with Ultrafuse® 316L obtain their final properties, including hardness and strength, through the catalytic debinding and sintering process. The catalytic debinding technology was developed and introduced by BASF and has emerged as the industry standard.
If you're using an UltiMaker S-line printer, combining BASF with the UltiMaker Expansion Kit, allows you to 3D print metal parts right in your home or office!
Because of the specialized catalytic debinding processs needed for this material, your printed parts will need to be shipped to a 3rd party for debinding and sintering. Then your final metal parts will be shipped back to you. If you'd prefer to be able to process your metal parts in-house, read on!
The Virtual Foundry - In-House 3D Printing and Post-Processing of Metal Parts
The Virtual Foundry offers an incredible solution so that everyone has the power to 3D Print and Sinter metal, ceramics and glass with simple equipment that everyone can afford!
Combine a common FDM 3D Printer with a common kiln and experience 3D printing pure metal 3D printing at home!
Affordable and Easy to Use, Here’s How printing with Virtual Foundry Filamet™Works:
-
The Virtual Foundry's Filamet™ is a revolutionary line of metal, copper, bronze, and ceramic filaments for Fused Filament Fabrication (FFF) Metal 3D Printing.
- With the combination of a common 3D printer and a programmable kiln, you can create durable and intricate metal 3D prints at home.
- This technology revolutionizes metal and ceramic 3D printing by combining traditional material strength with the simplicity of cutting-edge techniques, previously only available in industrial settings.
- Filamet™ delivers high-quality outcomes for various projects, making premium metal 3D printing accessible to all.
Have Questions About 3D Printing with Metal?
If you have any questions about metal 3D printing or are interested in 3D printing metal with your own FDM desktop 3D printer, feel free to reach out to us to help you discover the right combination of machines and filaments for your needs!
Email us at info@shop3duniverse.org to connect with us!